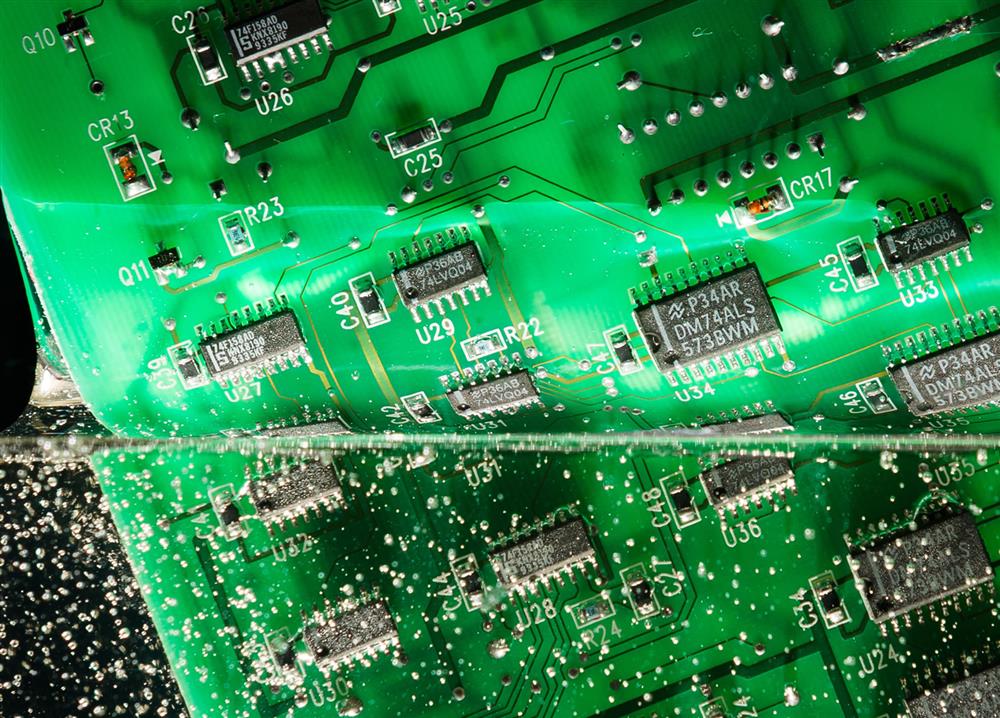
An important part of the PCB assembly process is ensuring the board is well protected once the components have been soldered and before the PCB is ready to be used. Part of this process, and one of the several ways to protect the board, is PCB conformal coating.
What are conformal coatings?
Conformal coating is a thin polymetric film that is added to the surface of a PCB in order to protect the board and its components. PCB conformal coating acts as a barrier for the board against any contaminants in its environment. Conformal coating can be applied in several ways, but the most common are through spraying, dipping or painting by hand and is usually made from material such as acrylics, silicons, epoxy or polyurethane.
Why do you need conformal coating?
PCB conformal coating is needed for several reasons, the most important of these being to protect the board and its components from any corrosion or electrical failures. The conformal coating also has high insulation protection resulting in closer conductor spacing.
As well as offering good protection for the PCB, conformal coating can also increase the strength between dielectric conductors as the minimum dielectric strength, particularly for acrylic conformal coating, sits at 1100 volts. This means the coating will not fragment or crack and provides strong insulation and protection meaning it can work with higher voltage gradients.
PCB conformal coating is essential if you want a circuit board that is durable, reliable and has a long shelf-life.
Which industries demand the use of conformal coating?
PCB conformal coating should be used as an essential, standardised part of the PCB assembly process for protection. Some industries demand this process takes place with the utmost precision. These industries include the likes of military, automotive, aerospace, automation, healthcare, and green energy applications. This is mainly due to the harsh conditions they’re exposed to and the importance of their role within the machinery.
As the industry and demand grows, PCB conformal coating is also being used in more day-to-day products such as electronic devices. Generally speaking, however, it’s mostly used for high end, specified products, such as those in the aforementioned industries.
What types of conformal coating are there?
There are several different kinds of conformal coating that can be used from a range of different materials. The most commonly used, and used at Ruiputuo, are acrylic and UV cure coating.
Acrylic coating
PCB acrylic coating is popular because it’s easy to use and apply, and dries easily at room temperature.
Acrylic coating offers good protection while being the most financially viable option compared to other coatings. Acrylic coating provides excellent mist, dust and humidity protection alongside a wider operating temperature range. It’s also easy to apply to a wide range of surfaces and substances, with excellent adhesion, further fuelling its popularity in the industry.
That being said, PCB acrylic coating doesn’t offer the strongest protection when it comes to chemical erosion, such as fuels.
Polyurethane coating
In comparison to acrylic coating, polyurethane coating offers fantastic protection against chemical erosion and under harsher conditions.
Urethane conformal coatings work as hard protective coatings offering great protection to boards that are exposed to excessive chemicals, alongside protection against humidity. Generally, polyurethane coating is used on applications such as motors, transformers and generators which work under harsh and high temperature conditions, and can be commonly used within the military or aerospace industries.
Polyurethane is a very robust form of coating. However, the disadvantage of this is its long curing time.
Hybrid coating
Hybrid conformal coating consists of combining a number of different chemical bases in order to create the desired coating for your application. For example, polyurethane can be combined with silicone to help improve its resistance under higher temperatures.
Hybrid coatings tend to be solvent based and bring additional benefits that standard silicon coatings wouldn’t have, such as enhanced temperature endurance and high chemical resistance. It’s also easy to apply.
Depending on what your product is, and the environment it’s going to be exposed to, a range of hybrid coatings can be used to help enhance its performance.
Silicone coating
Silicone PCB coatings tend to be the most flexible coatings used within the industry, as they’re able to withstand high and low fluctuations of temperatures, meaning they give good protection in a range of harsh environments. Silicone coatings also provide good dielectric strength, which means they work as a good insulator for boards.
While they are able to withstand wide ranging temperatures, silicone PCB coating doesn’t offer protection as strong against corrosion or humidity as its counterparts.
Water-based coating
Water-based coatings are by nature safe products which allow consumers or companies to reach their emission targets due to their low odour and VOC emissions. Water-based coatings are based upon their counterparts acrylic and polyurethane to offer similar performance properties. As water replaces the majority of solvent within the system, this form of coating improves both environmental and operator safety.
Water-based coatings cure by the evaporation of water and offer a good level of protection.
UV cure coatings
UV cure coatings are another example of a hybrid coating, with a single layer of coating which cures very quickly under the exposure to UV light. It offers the fastest curing time of all the coatings available.
It can be applied using specialist spray equipment and offers good chemical protection to the board. However, due to their curing process it can be difficult to remove from boards and provides reduced flexibility.
2k coatings
Another example of hybrid coatings are 2k coatings, which combine properties of resin into the conformal coating process. The properties used from resin are some of the best, and allow for similar high performance to its counterparts at an affordable price.
2k coatings also provide a high level of protection to moisture and for boards being used in harsh environments.
How are conformal coatings applied and cured?
Ensuring your conformal coating is applied and cured correctly is extremely important. You can choose the best coating for your board, but if this is not applied and cured directly, your board will not be protected and perform as highly.
As discussed above, some PCB coatings have different levels of thickness, alongside different adhesive abilities when sticking to boards.
There are several methods to apply conformal coating:
and coating manually with a brush
praying
sing an aerosol
Dipping
sing a selective coating machine
Brush coating is often done manually. The concern with this is whether the coating will be over applied, which can lead to issues, so this must be done with precision.
Aerosol application can be cost effective and easy to use for smaller products. Aerosol application is best done within a clean spray booth to avoid any contaminates and ensure it’s well ventilated. Interestingly, despite common practice to shake an aerosol before use, this should not be done in the aerosol application of conformal coating, as this can cause bubbles to be added to the aerosol and therefore to the board. The aerosol should be applied at a small distance, approximately 20 mm away with the board being continuously rotated in order to create an even coating.
A machine can also be used for both dipping and selective coating, which can often be more accurate. Dip coating can be a slow process, wherein the board is slowly dipping into the coating itself. While this ensures the board is fully coated, you also need to ensure any areas you don’t want to be covered are masked beforehand. However, masking cannot be dipping into the coating more than once, so this can be time consuming to replace.
Selective coating is the most efficient way to apply conformal coating to PCBs. The machine allows you to select which areas of the board you would like to be covered, and with what level of thickness. While this can be an efficient and cost effective way to coat PCBs, if you don’t already own the right machinery, this can be a more expensive process.
There are several different ways to cure conformal coating, depending on the type of coating that has been used. The most common of these is to apply heat to the boards to speed up the process of evaporation of the solvents. However, if you’ve used a UV conformal coating, UV light must be used in the curing process to create a chemical reaction that causes the coating to cure almost immediately.
Lastly, moisture cure coatings require curing by moisture from the atmosphere. Humidifiers and other appliances can be helped to speed up this process.
What are the standards for conformal coating?
Throughout the industry there are standards that must be adhered to for conformal coating inspection and testing. This is particularly important in industries such as aerospace and the military.
The test for these standards and inspections all require flat coupons to be coated with the specified conformal coating and exposed to humidity and various temperatures in order to assess its properties. This is particularly important for boards that will be used under harsh or within corrosive environments.
Military companies and industries have their own standards which must be adhered to (MIL-I-46058C). While this is no longer actively used in new designs, it is still a requirement for the military industry. This must be done by a military approved lab and when complete, the products will be added to a Qualified Product List (QPL). When MIL was discontinued and inactive in the industry, an alternative was made: IPC CC-830. Unlike MIL, an independent laboratory doesn’t need to be used and a product will not have a QPL at the end of the process.
The International Electrotechnical Commission (IEC 61086) is similar to MIL in its requirements, however the tested products don’t maintain a QPL.
UL94V0 is a flammability test for conformal coatings which are scored from V–0 to V-2. V-0 is the highest classification whereas classifications like V-1 and V-2 indicate they burn for longer. In addition to the flammability test, UL746E is made of dielectric breakdowns to denote products that can be safely used on products that are required to meet UL safety standards.