Feedback guides decision-making. Not only do we see this in circuit networks but in all aspects of electronics manufacturing. The best feedback arrives when designs are highly modular: the later feedback needs to be incorporated, the more disruptive (albeit necessary) the changes. Many parts of PCB development can only be verified after manufacturing – take EMC testing, for instance – but some of the best feedback loops can be adopted before a single panel enters fabrication.
PCB layout review is a multi-disciplinary analysis of preparedness before initial manufacturing is set to begin. Without a doubt, PCB production is an iterative design and manufacturing process, but carefully evaluating the layout will accelerate the development process while circumventing common design issues that can arise.
Sample of Layout Review Items | |
Placement | Routing |
|
|
Placement and Routing: The Twin Threads of PCB Layout Review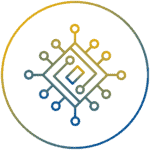
After the layout is finished, product development teams will want to confer to discuss the design from a production standpoint. With DFM, layout designers will already have established communication between the engineer and manufacturing manager to ensure the layout maximizes performance, design intent, and producibility. Yet precisely-followed design rules may still leave a board in an unoptimized state. More esoteric best layout practices (does a signal return path cross a split plane/plane gap?) may not be captured by design rule checks. Board layouts adapted from DFT or with an extensive revision history may have features that are less applicable for manufacturing and require correction.
The prevailing mentality is “do it right, or do it twice (or more).” A board lacking focused design will require additional layout revisions while turnaround time increases and money is lost on unsatisfactory products. VSE values layout reviews as the cornerstone of agile manufacturing for NPI that minimizes the total time for our customers to receive completed boards.
Our PCB layout review will focus on a few key aspects of the board:
Placement: Component placement will want to consider not just where components should be placed for best performance but also how their location will affect later manufacturing steps. Are connectors easily accessible, or are they surrounded by tall profile components that may make plug insertion/removal difficult? Are solder shadows present that could impact automating soldering processes, requiring manual work on small or short components that can be less effective and more costly? Can test points be reached by automated or manual measuring tools, or are they obstructed? Clearance issues like these underline how many standard design rulesets cannot alone encompass all of the concerns of DFM/A/T.
Routing: Routing issues tend to be observed less during manufacturing and more during testing and performance metrics. ECAD tools are robust enough to cover the various shapes, groups, and conditions of the boards’ nets. However, routing not accounting for potential EMI/EMC interactions between traces and components may result in fabricable boards that fail during runtime. Our engineers take note of high-speed signals and large inductive loads (namely inductors in switched-mode power supplies) that can influence nearby signals through induction. Conversely, sensitive lines will also receive extra consideration of how nearby signals may interact with them.
The Impact of Documentation on Producibility
A perfectly laid out board may still suffer from poor documentation. Those on the manufacturing floor rely on unambiguous directions to ensure the design intent carried from the initial design documents to the layout is expressed in the final product. Artwork not only needs to convey visual information accurately but also processes like surface finish when a design contains particular requirements. As a turnkey PCBA solution, we ensure that your documentation is concise and thorough for an uninterrupted transition to manufacturing.
Documentation also extends to the board itself. Clear and legible silkscreen will greatly aid technicians in locating components and test points during manual processes. It’s easy to sit at a computer screen where board files enable dynamic zooming and find a silkscreen acceptable; a static printed image of Gerber artwork does not possess this ability. Designers should view a board from a 1:1 scale on the screen to determine whether a silkscreen is easily readable without visual aid. Designers should also check these silkscreen elements:
Pin 1 indicator or polarity/orientation markers. Many components and connectors can be installed and soldered in two or more orientations, resulting in unintended circuit layout in all but the simplest passive components (and even then, it may cause issues). For components like electrolytic capacitors, this could pose damage to the board and a safety hazard to technicians or operators. Have pin 1 indicators visible and unobscured by component bodies.
Reference designators. Designators should be placed as close as possible to the component in question, and designers should utilize visual elements on the silkscreen layer (lines, arrows, etc.) to associate components and designators when there is ambiguity. Use only one vertical and horizontal orientation for reference designators. In densely populated assemblies, the designators for “straightforward” components like resistors, non-polarized capacitors, etc., can be hidden in favor of polarized components, ICs, connectors, and test points.
From Review to Debut: Your Contract Manufacturer Covers NPIs And Beyond
DFM is a broad design methodology category, and best practices may shift with the scope of the production. A layout for an NPI may be focused on minimizing the turnaround time to get prototypes or finished products back to customers’ hands as quickly as possible. High-volume production, meanwhile, will want to focus on reducing per-board costs as much as possible. A longer layout time can minimize feature redundancy at the board level – for instance, reducing via count with a granular analysis of trace routing – and improve board quality by removal of failure points during manufacturing or service life.
Ruiputuo has mass production facilities located in Guangdong Province, China. And pre-production analysis doesn’t end with PCB layout reviews: our engineering team can review or design enclosures for form, fit, and function as part of our comprehensive box-build services. We ensure that every part of your electrical system meshes to maximize performance, even in the most complex design.
At Ruiputuo, we’re a team of engineers committed to building electronics for our customers. Alongside our valued manufacturing partners, we aim to deliver nothing less than the highest quality in PCBA engineering, manufacturing, and testing for life-saving and life-changing applications.